Advanced metrology can help overcome the impending semiconductor process gas shortages
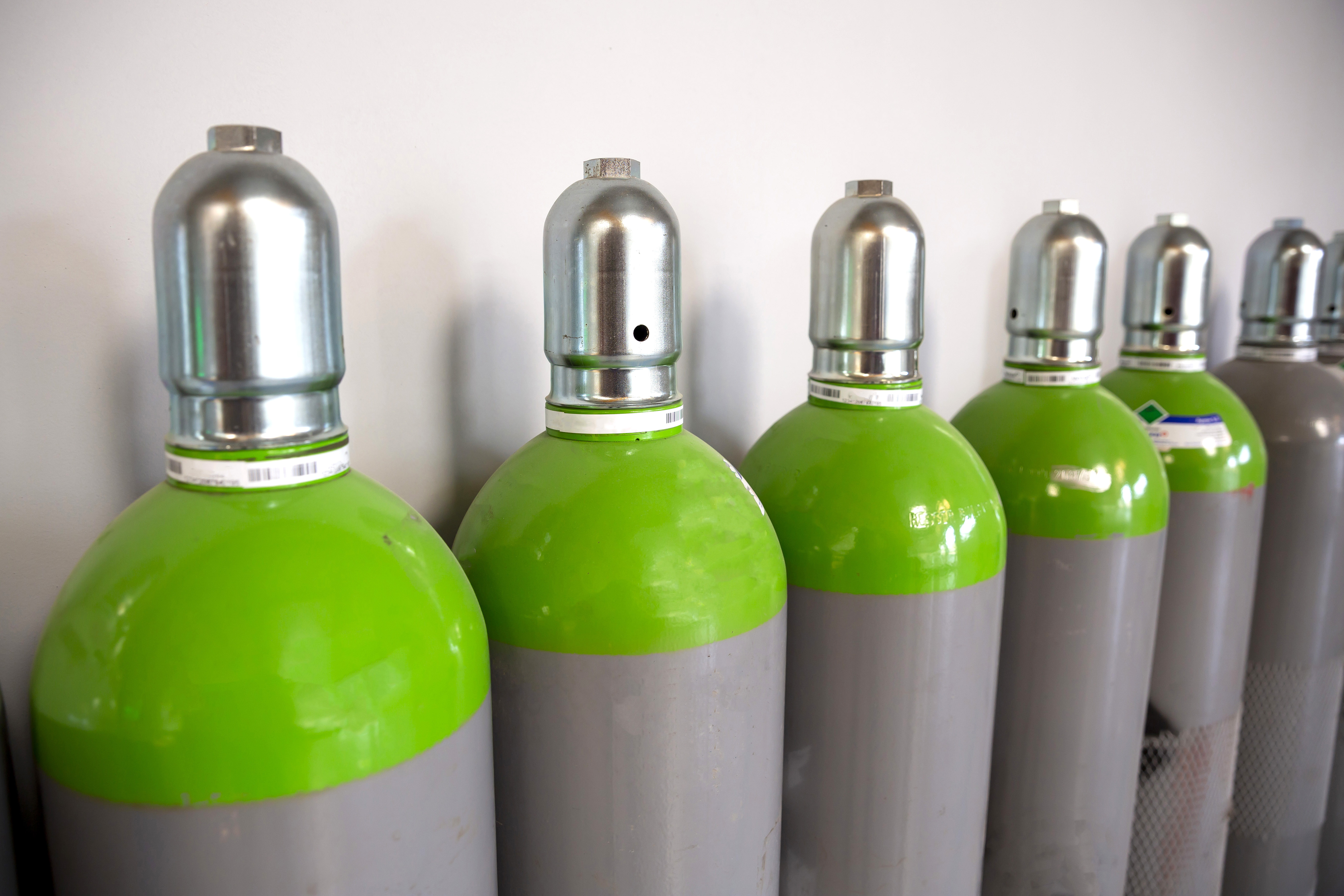
Challenges related to the semiconductor shortage have been well documented. But one emerging issue is generating less attention: the forecasted shortage of certain process gases critical to advanced process control.
3D NAND memory is found in a growing number of devices, including phones and PCs, as well as in cars and data centre computers. As the demand for memory continues to escalate, manufacturers are responding by adding more layers to their 3D NAND chips.
The rising demand for memory, and these additional layers, are driving higher use of tungsten hexafluoride gas, WF<p-sub>6<p-sub>, in the chip manufacturing process, which is expected to lead to a supply storage by 2024. Growth in 3D NAND production is also driving demand for nitrogen trifluoride (NF<p-sub>3<p-sub>), which is similarly expected to be in short supply within a few short years.
This comes on the back of well documented helium shortages over the past 2 years. However, while helium consumption in the semiconductor industry represents only ~5% of global production (most of the helium is used for medical imaging (MRI) applications), specialty gases like WF<p-sub>6<p-sub> are the primary gases used in semiconductor manufacturing.
Advanced metrology platforms like Atonarp's ASTON will help to answer the process gas shortage problem by enabling in-situ monitoring that can optimize the use of WF6 gas consumption.
As the number of layers grow in memory devices, tungsten is used to create the word lines. It is applied as WF<p-sub>6<p-sub> gas and has the ability to create very good conformal coatings, so that it can get into the minuscule nooks and crannies of the multi-layered 3D NAND memory device stacks.
To apply the tungsten, the gas used is WF<p-sub>6<p-sub>, it decomposes to leave the tungsten metal, and produces hydrogen fluoride (HF) gas as a typical byproduct.
A major challenge is that optical emission spectroscopy typically cannot be used for in-situ management of tungsten deposition as an ALD process uses no-plasma or a weak remote hydrogen plasma. Similarly, residual gas analyzers (RGA) have their filament ionization sources attacked by the highly corrosive by-product of HF gas, rendering them unusable for volume production in-situ metrology.
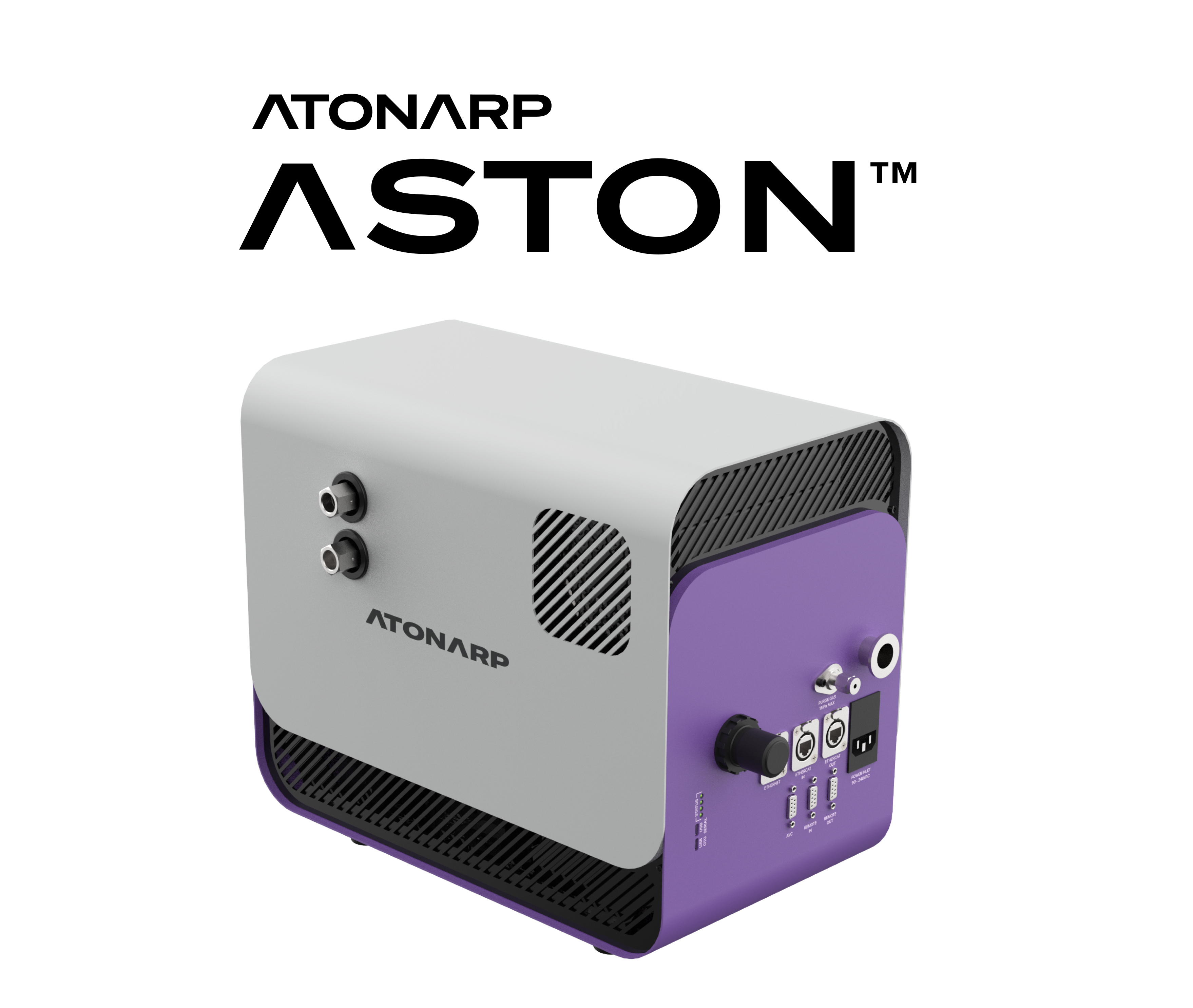
These conventional solutions cannot provide the in-situ monitoring that is required to optimize the usage of WF<p-sub>6<p-sub> in ALD cycles. Advanced metrology platforms, including Atonarp’s Aston with its integrated plasma-ionization solution, help to answer this problem. It is the only system today that enables in-situ monitoring that can optimize the use of WF6 gas consumption.
With gas shortages forecast in the next few years, the efficiencies provided by Aston can reduce dependence upon WF<p-sub>6<p-sub> and other process gases likely to be in short supply. By running processes smarter using Aston in-situ metrology, the impact of any shortages can be minimized – and, of course, overall costs are reduced.